多摩冶金
70年の歴史
熱処理一筋70年のあゆみを紹介します。
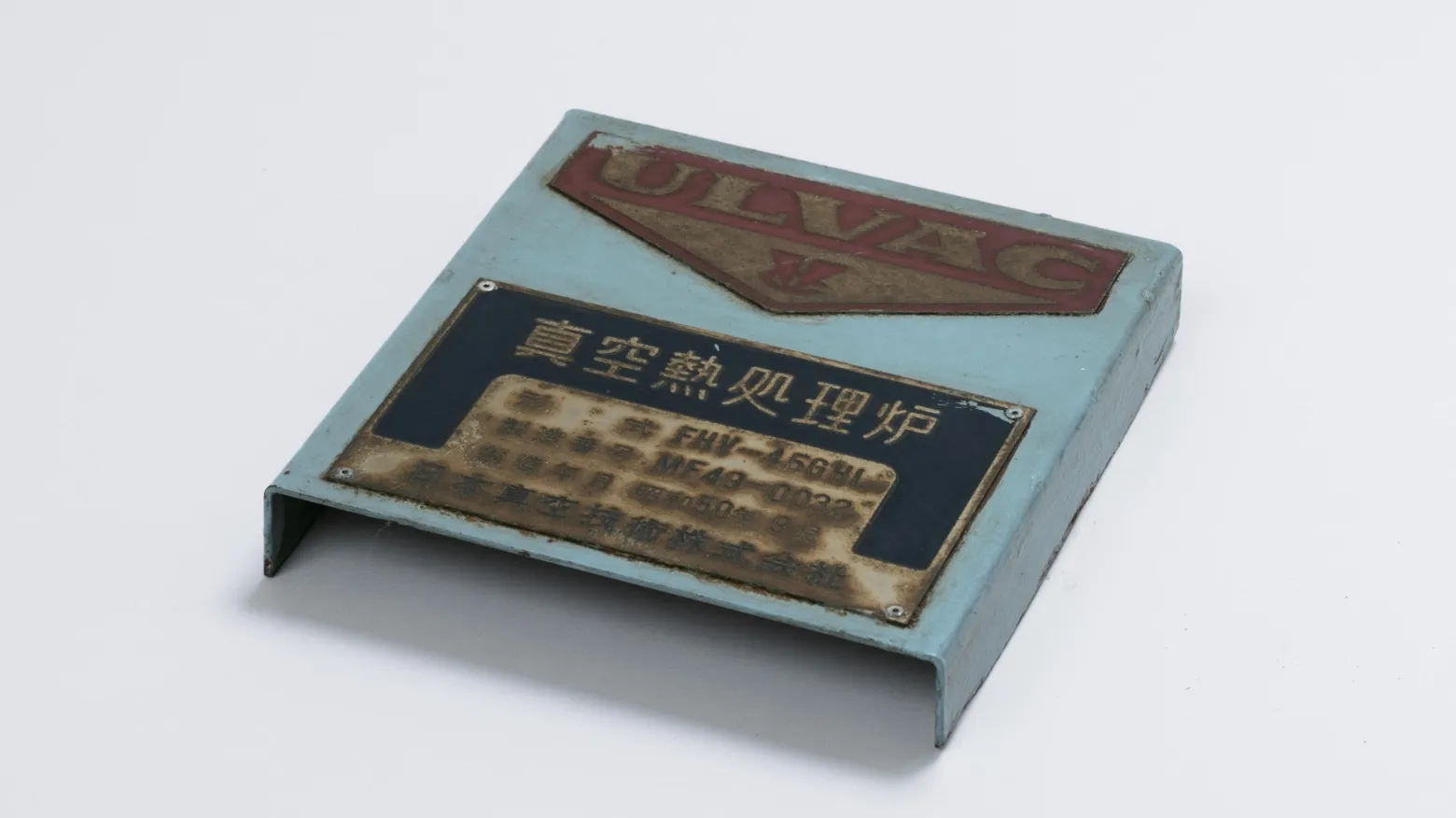
熱処理一筋
70年のあゆみ
加熱と冷却の巧みな調整により、金属を軟らかくも・硬くもでき、強度や耐久性までも自在に操れる特殊加工技術『熱処理』。その歴史を遡ると、鍛冶職人による日本刀造りでも応用されており、私たち日本人の文化にも深く根付いています。
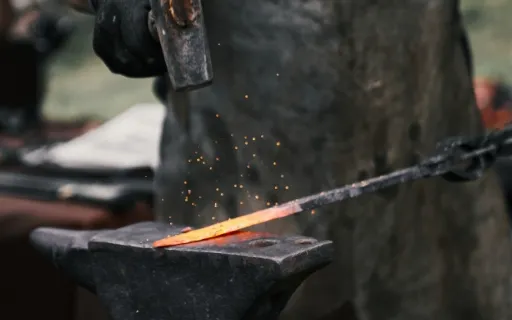
現代では、自動車や航空機などの乗り物から精密機器、機械工業に至るまで、経済や産業の発展に密着した技術として広く認知されており、中でも航空機などの高い精度が要求される分野においては、切り離すことのできない重要な技術として評価されています。
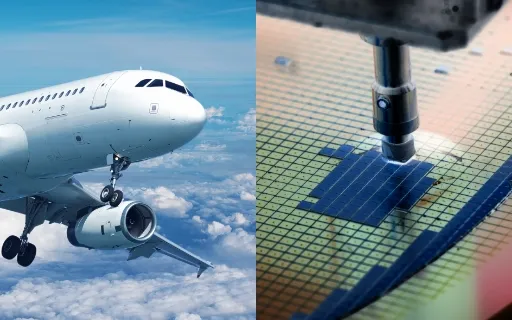
私たち『多摩冶金』は1951年の創業より、日本経済の発展とともに成長を遂げてきた熱処理のプロフェッショナル集団です。
長い歴史の中では、不況や自然災害などに伴う苦境も経験してきましたが、熱処理技術が世の中にもたらす重要性を自負し、常に「技術、人、工場」を磨いてまいりました。
そしてこれからも、「Mission」・「Vision」・「Spirit」を中核に据え、人と人とのつながりで技術、文化、想いを次世代につなぐことに日々感動し、そして共感しながら明日を創り続けていきます。
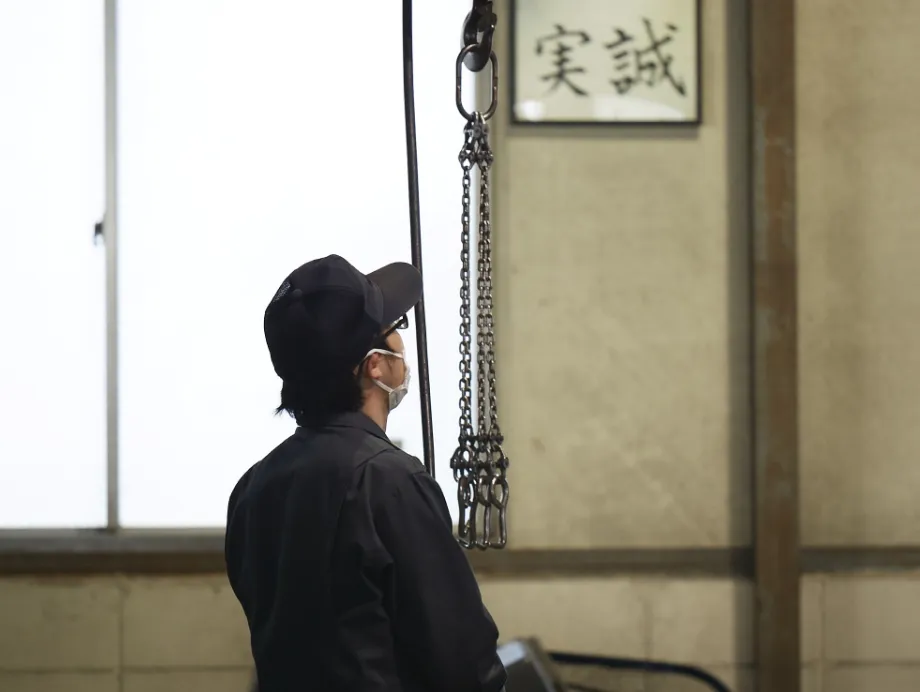
多摩冶金『創業者』
大正5年(1916年)東京都生まれ、早稲田大学理工学部卒業後、海軍技術大将を歴任。終戦を迎え、多摩冶金株式会社の前身でもある、多摩熱処理有限会社を立ち上げました。当時は手作業で熱処理の窯を作り自転車部品の熱処理をしていましたが、高度経済成長時代を背景に、技術や会社の発展に邁進し、多摩冶金の基礎を創りました。立ち上げ当初より、妻である故・山田孝子は、会計から納品まで裏方を支え、二人三脚で会社を盛り立てました。
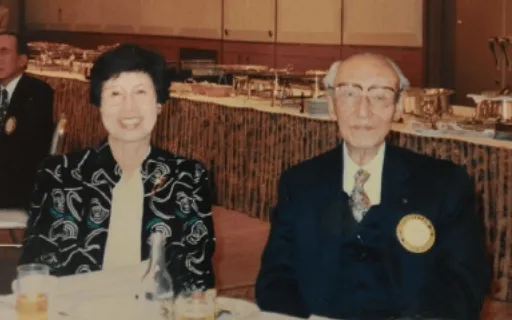
TAMAYAKIN
の沿革
戦後復から現在、
そして未来へ
世界の産業を支え続けてきた
多摩冶金の挑戦の歴史をご紹介します。
創業期|1951~
「戦後復興を支えろ!」
創業者の奮闘沿革
戦後の復興の混乱期の中で創業し、
高度経済成長期においてもものづくり大国日本を支えるべく奮闘した時代である。
多摩熱処理有限会社、
武蔵野市で創業
創業者・山田啓、多摩熱処理有限会社を資本金100万円で創立し、東京都武蔵野市中町において業務を開始する。

創業期の武蔵野工場
早稲田大学の理工科応用化学を卒業後、吉林人造石油へ就職した山田啓は、太平洋戦争開戦に伴い海軍技術士官として招集され、海軍工廠にて火薬製造に携わった。
終戦後は、廃工場となっていた父親が所有する多摩絶縁体有限会社の軍事工場を活かし、持ち前の化学知識を用いて熱処理事業をスタート。現在へとつながる商いの基盤づくりを行うこととなる。
当時の武蔵野市には、ゼロ戦など軍用機のエンジンを製作していた中島飛行機の解体に伴い、優れた技術力を誇る職人たちが独立し、手腕を振るう小さな機械工場が数多く存在していた。
その影響もあり、自転車の歯車などの熱処理から手がけるも、瞬く間にそのニーズは自動車部品や機械部品にも派生。戦後の混乱期に、復興の礎となる製造業を支える存在へと変貌を遂げていく。
手製で組まれた熱処理炉を次々と増設し、小さな工場には収まりきらないほどの受託製品が入り口付近に積み上げられ、その規模からは想像し難い数の熱処理をこなし急速に発展した。
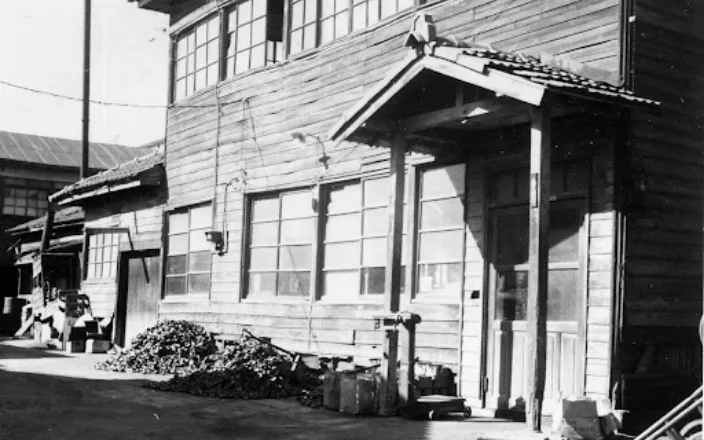
創業期の武蔵野工場
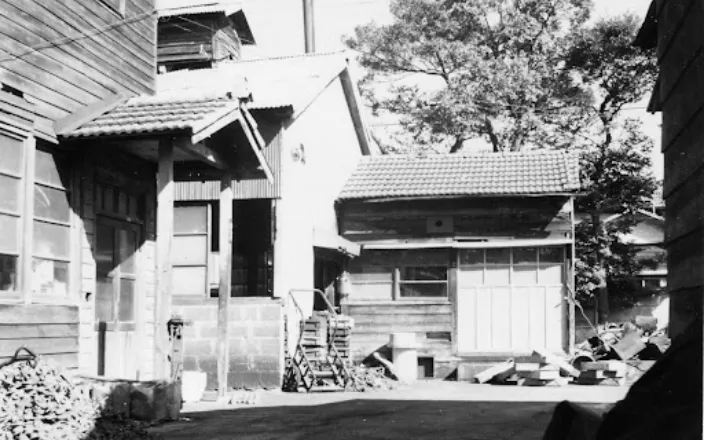
創業期の武蔵野工場
詳細を
宅地化が進み、移転へ。工場拡大、いざ武蔵村山市へ!
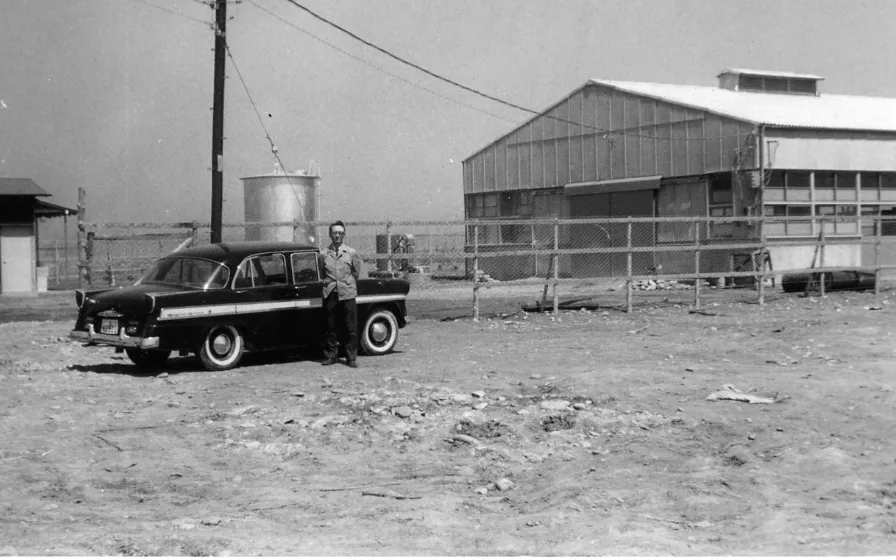
創業期の武蔵野工場
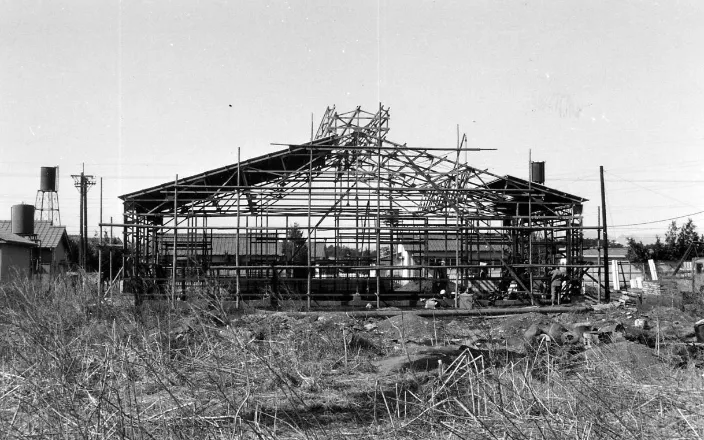
雰囲気工場建設の様子
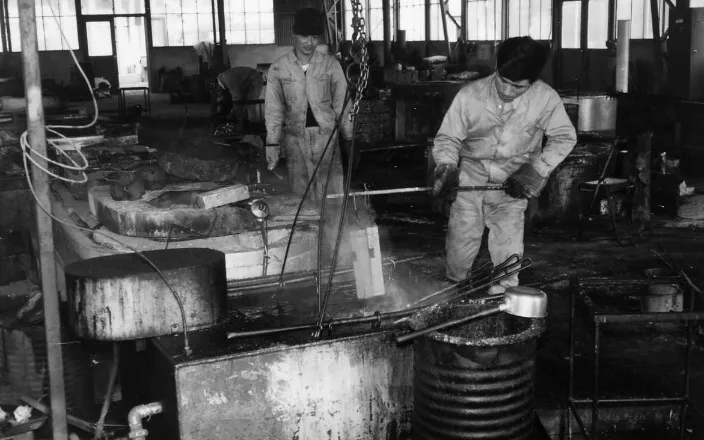
雰囲気工場建設の様子
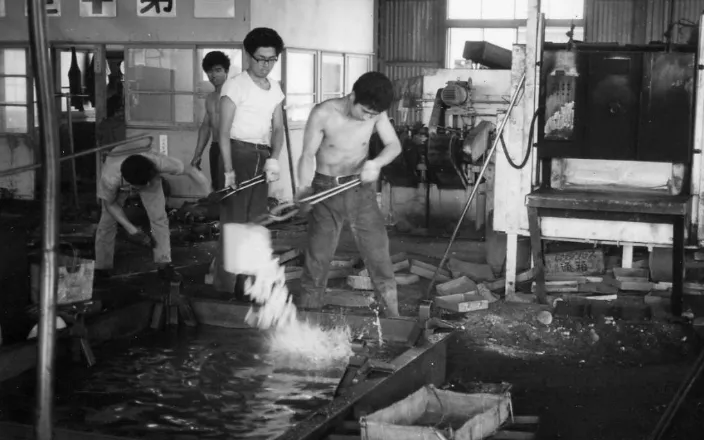
塩浴作業風景(昭和40年頃)
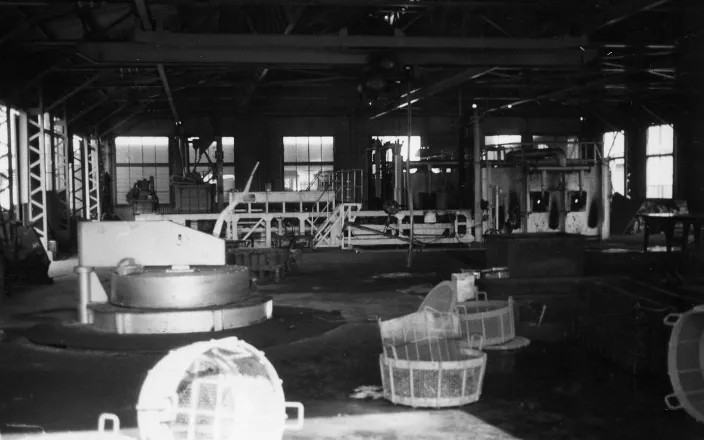
調質作業場(現ユニケース炉付近)
詳細を
自動車業界への参入、認定工場へ
日産ディーゼル工業(株)、(株)小松製作所、キャタピラー三菱(株)等の熱処理認定工場となる。
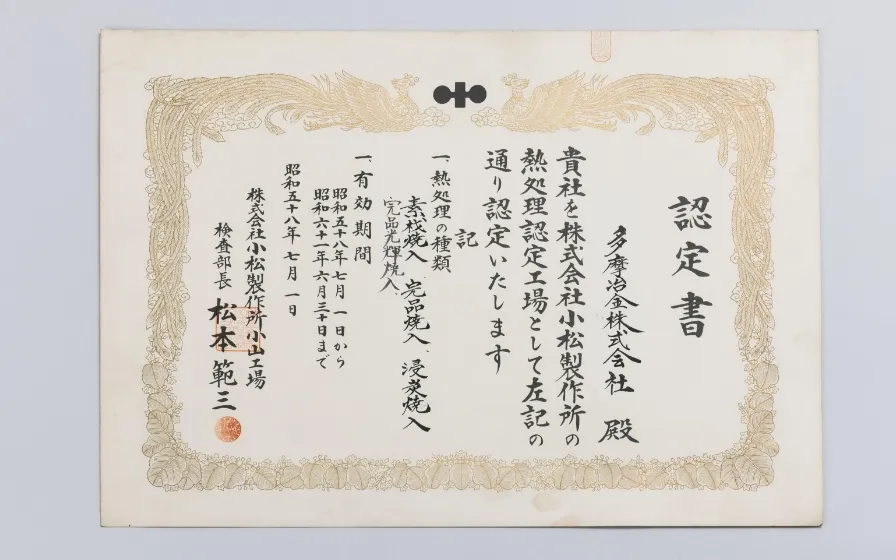
当時の(株)小松製作所認定書
社名変更、そして多摩冶金株式会社の誕生
多摩冶金株式会社に社名変更並びに組織を変更する。創業者の妻、山田孝子も副社長として財務を担当し、夫婦で経営を切り盛りする。
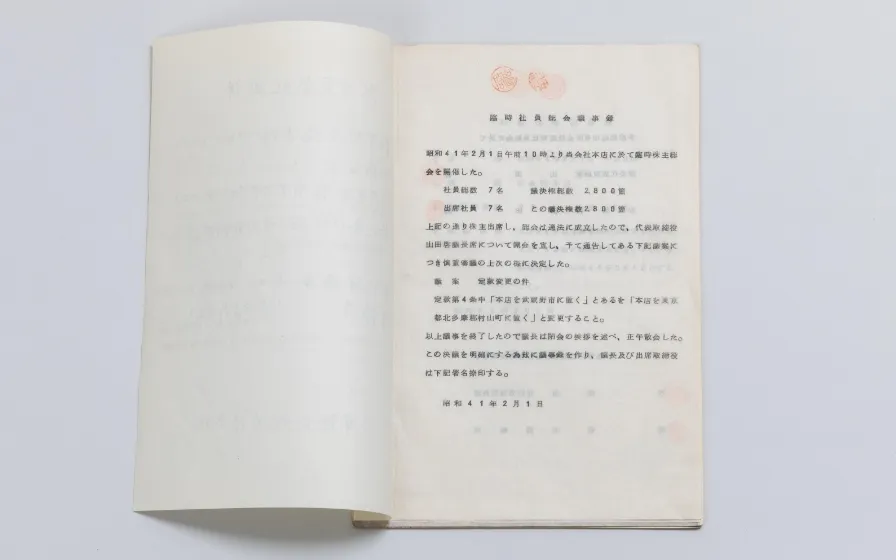
現在の武蔵村山市(当時の東京都北多摩郡村山町)への移転の時期に変更された定款(昭和41年)
他業種・多品種・小ロット生産への挑戦
自動車・建機部品の量産形態から多業種にわたる多品種小ロット生産形態に移行する。
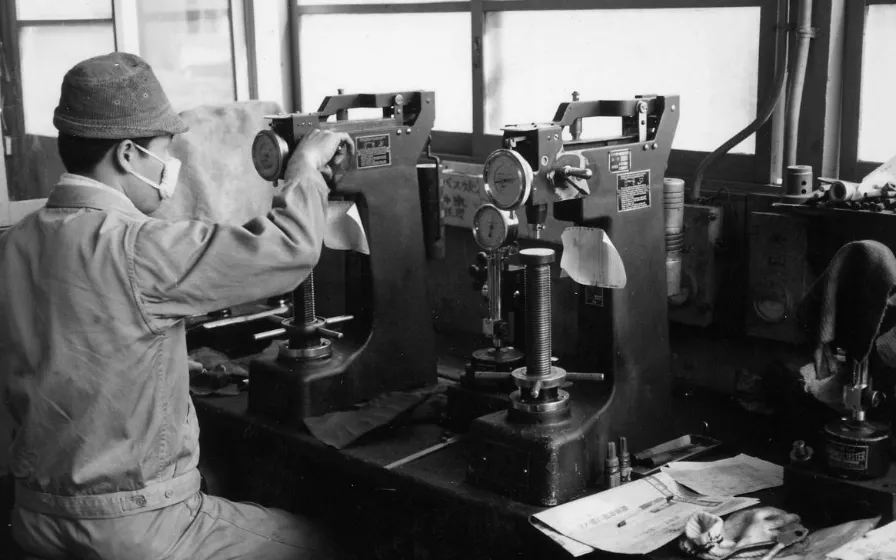
検査場の様子
大手自動車メーカーの下請けとして、複数社の認定工場となった多摩冶金であったが、高度経済成長期に突入し、熱処理も短納期・低価格を厳しく求められるように。「大手企業の下請けでは、自分たちの持ち味が活かせない」と考えた創業者 山田啓は、付加価値の高いサービスを提供することで、利益率の高い経営体制を確立すべく、多品種・小ロットの生産形態へと移行を決意。
大手企業の量産品よりも、地域のお客様に目を向け、「ネジ1本から、難易度の高い製品まで」を合言葉に、それに見合った設備投資も実行し社内体制を確立していく。「時代に挑戦していく」この姿勢が顕著に表れる改革の一つとなった。
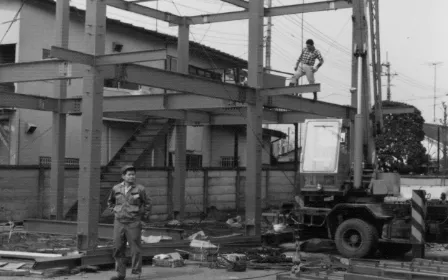
事務所棟建設(1982年4月完成)
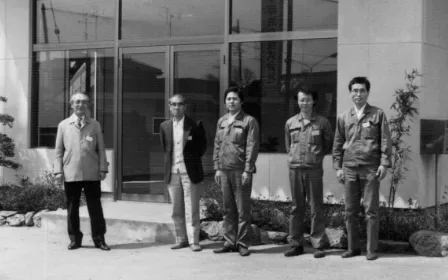
創業期の方々
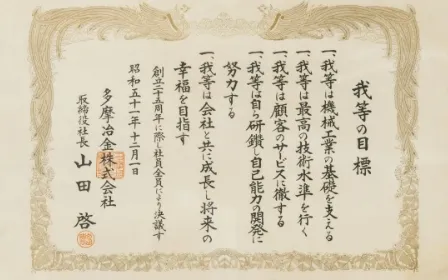
我等の目標
詳細を
目指せ、最高の技術水準!真空炉の導入
真空熱処理炉を導入。高付加価値、精密部品生産形態へ移行する端緒となる。以後、新型の真空炉を順次増設。
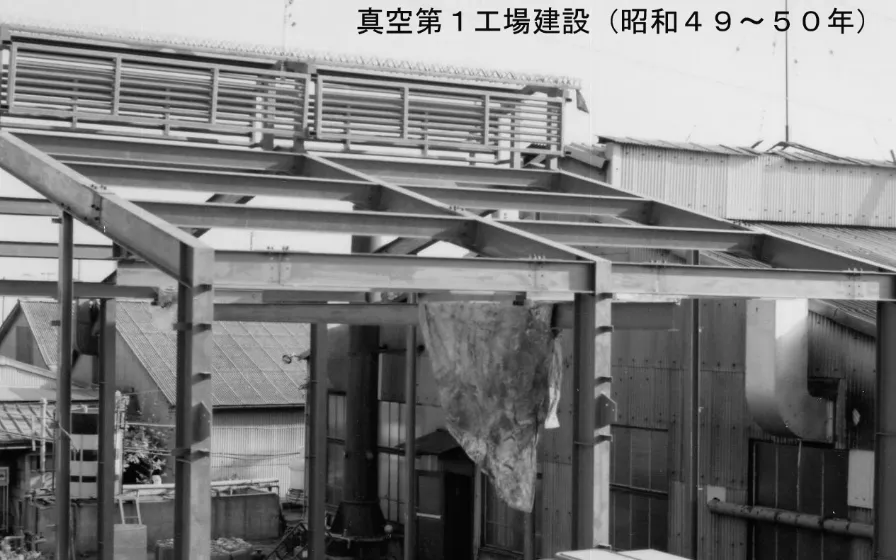
真空第1工場建設(1974〜1975年)
技術の進歩により工業用真空炉が開発され、工業的に真空熱処理が利用できるようになった。当時真空炉は非常に高価な設備であったが、山田啓は最先端の技術を取り入れることを決断し、他の同業者に先んじて初めての真空炉を導入した。真空熱処理は酸化せずに高温を利用でき、金型や精密部品の熱処理に適していた。顧客にとっては、新しい分野の金型や部品製造への道が開けたため、広範囲の顧客からの注文が殺到。すぐに1基だけでは間に合わなくなり、2号炉、3号炉と続けて導入したほど。これにより、さらなる飛躍の原資を得ると同時に、名実共に「多品種・小ロット、付加価値の高い熱処理は多摩冶金」という、明確な存在価値を示すこととなる。
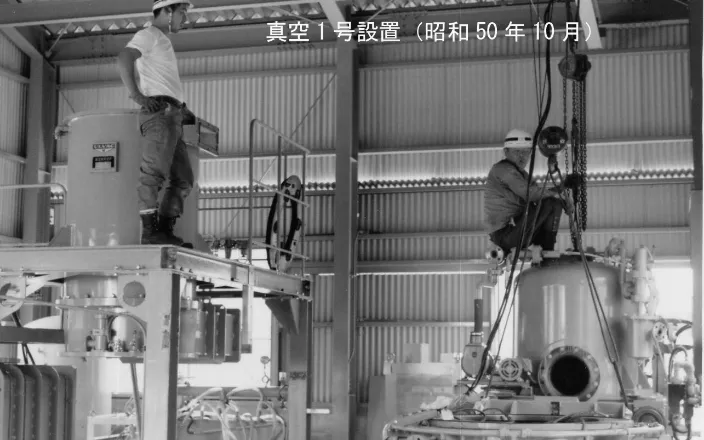
真空1号設置(1975年10月)
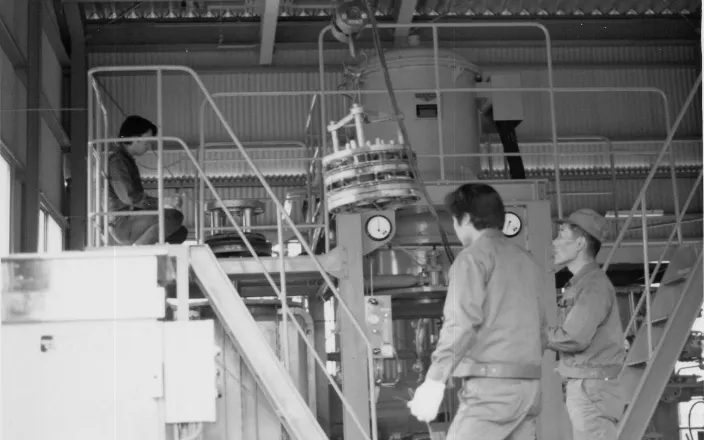
真空1号試運転
詳細を
さらなる技術開発、試行錯誤への道
イオンプレーティング装置を導入し、生産体制の一層の充実を図る。
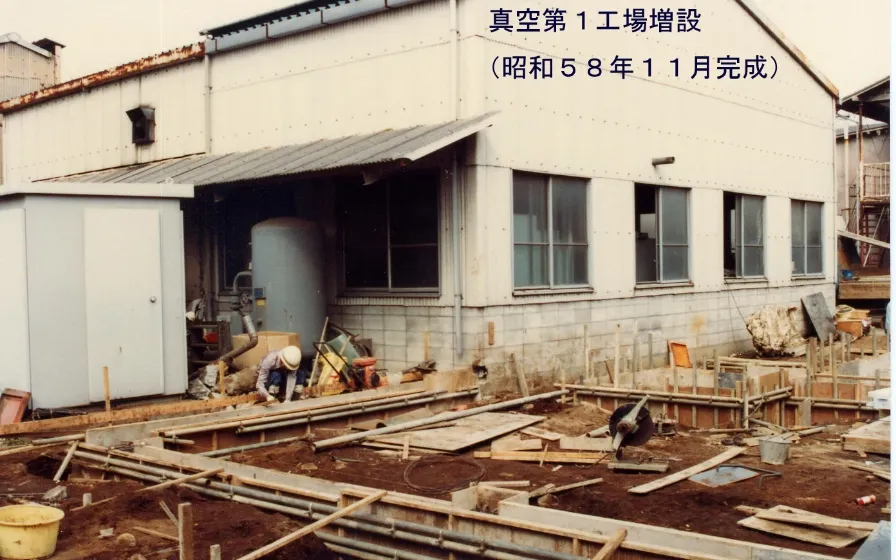
真空第1工場増設(1983年11月完成)
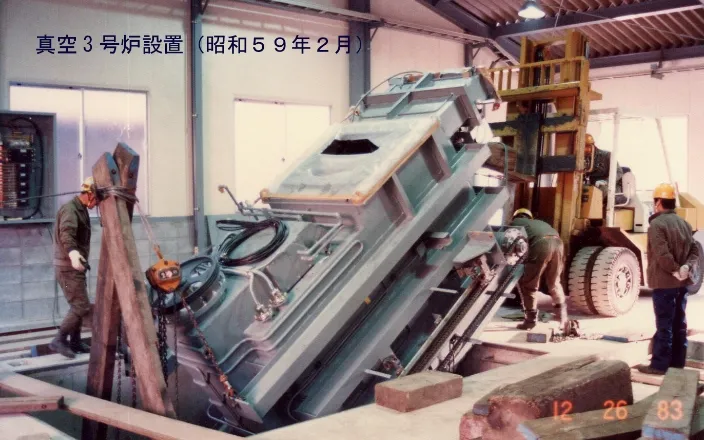
真空3号炉設置(1984年2月)
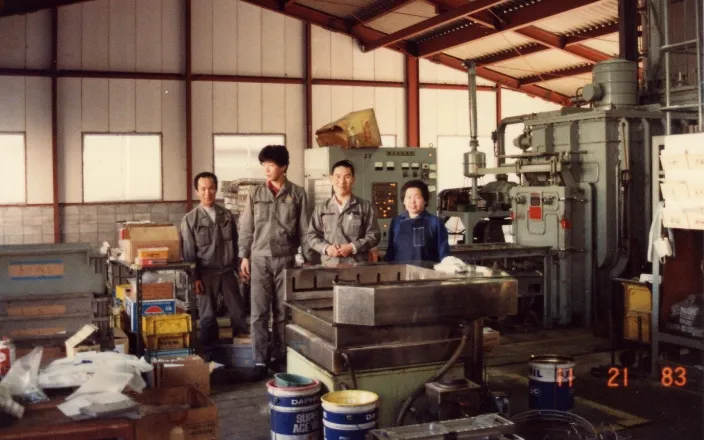
真空第1工場の様子
詳細を
第一次成長期|1988~
「空飛ぶ品質、空飛ぶ熱処理!」
航空機業界への入り口
バブル崩壊の景気不安やデジタル化など、世の中の動きが大きく変化した時代。
多摩冶金はいよいよ航空宇宙産業への一歩をスタートさせる。
初の熱処理認定を取得
IHI(石川島播磨重工業(株))に納入される航空機エンジン部品(V2500)の熱処理認定を取得。MIL規格品等の生産体制整備の端緒となる。
以後、イーグルEG&Gエアロスペース(株)(MIL-H-6875)、IHI航空宇宙事業本部(アルミ合金)、日産自動車(株)宇宙航空事業部・現IHIエアロスペース(MIL-H-6875)の特殊工程認定を順次取得する。
2代目社長であり元会長の山田仁が、多摩冶金に入社したのは1987年11月のこと。入社当初より海上自衛隊で培ったパイロットの経験を活かし、飛行機への熱い情熱を持って航空機産業への開拓に単身で挑む。
航空機産業への参入は、「多品種小ロットで高付加価値」という会社の方向性とも合致していたが、半面、その製造への理解や見合った生産体制を持ち合わせていない企業には、門戸自体が開かれない。山田仁は、インターネットなどの情報網がない中で、必要とされる品質管理、設備管理体制や人材教育などの情報を、前職で培った人脈やつてなどあらゆる手法を活用し‟足”で稼ぐこととなる。
苦戦を強いられる状況でも、航空機産業・飛行機への高いモチベーションで乗り越え、わずか入社1年弱でIHI(株)の熱処理認定を取得。山田仁が切り開いたこの第一歩が、現在の航空機産業に強い多摩冶金の礎となり、3代目社長・山田毅に引き継がれていくこととなる。
詳細を
中国より研修生を迎える
中国から日本の熱処理を学ぶために、若手技術者が毎年1~2人来日し、1年間研修期間を過ごす。11年続け、合計16人の若手中国人技術者を輩出した。そのうち3人が再度来日し、以後社員として活躍する。
中国の中でも優秀な大学を卒業し、熱処理や金属を専攻してきた人材が送られてきた。
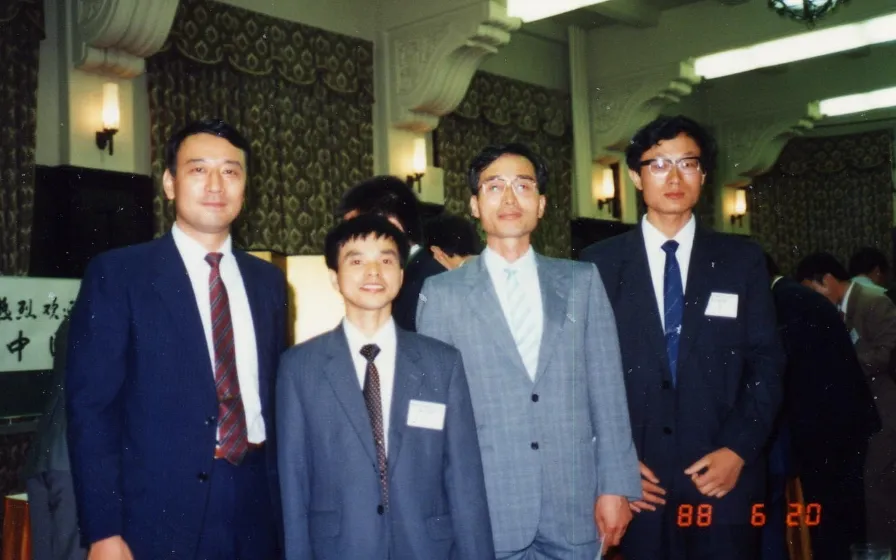
研修生一期生、初来日当日の記念写真
学士会館にて研修生1期生(左2番目:朱、左4番目:白)を挟むように2代目・山田仁(左1番目)と佐藤総務グループ長(左3番目)
自然環境を考えた技術の選択
炭化水素系真空洗浄機を導入し、オゾン層破壊物質である塩素系有機溶剤を全廃する。
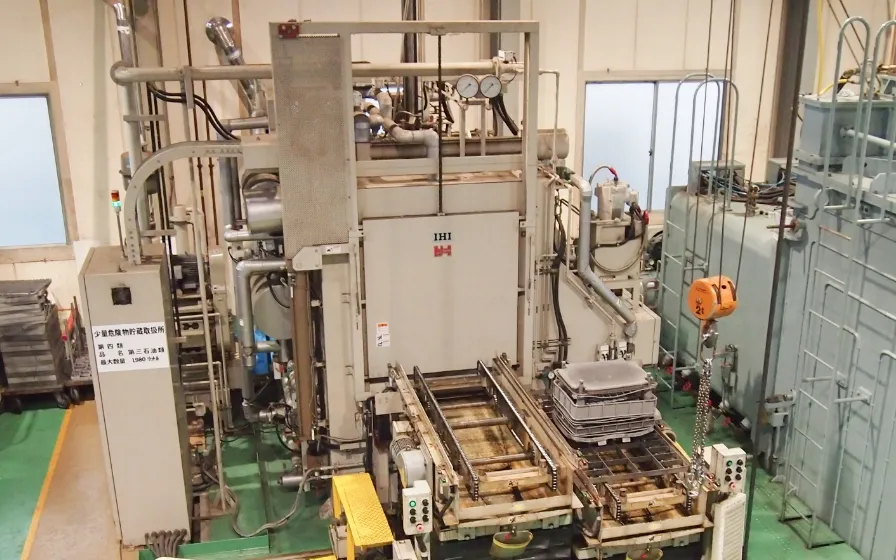
2台目に導入した炭化水素系真空洗浄機 VW2
2代目社長就任、
パイロットの目指す熱処理
前職の海上自衛隊ではパイロットを歴任した2代目社長・山田仁が社長へ就任。同年、自衛隊時代の同期であった間宮一は工場長に就任。
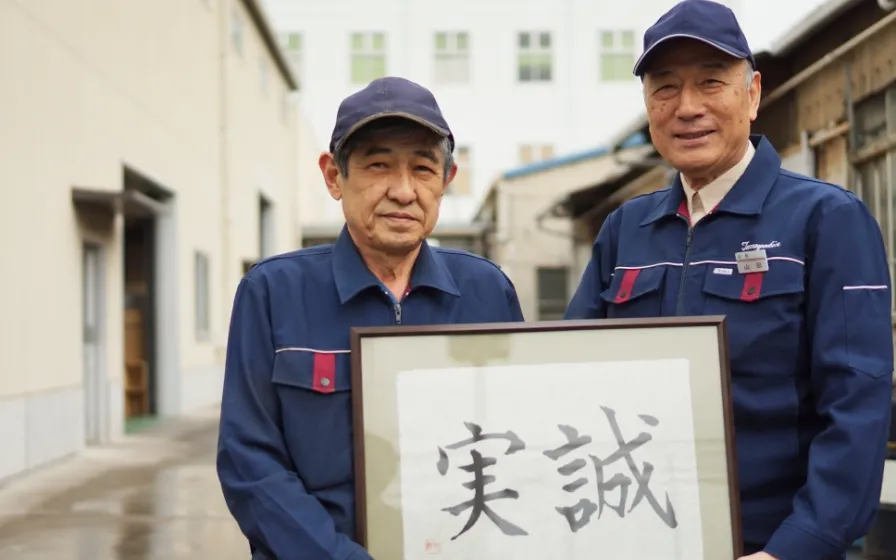
開拓期を引っ張った2代目社長(右)と工場長(左)
航空機用アルミ合金熱処理炉を設置
航空機用アルミ合金熱処理炉を設置。航空機用アルミ部品の熱処理を開始する。
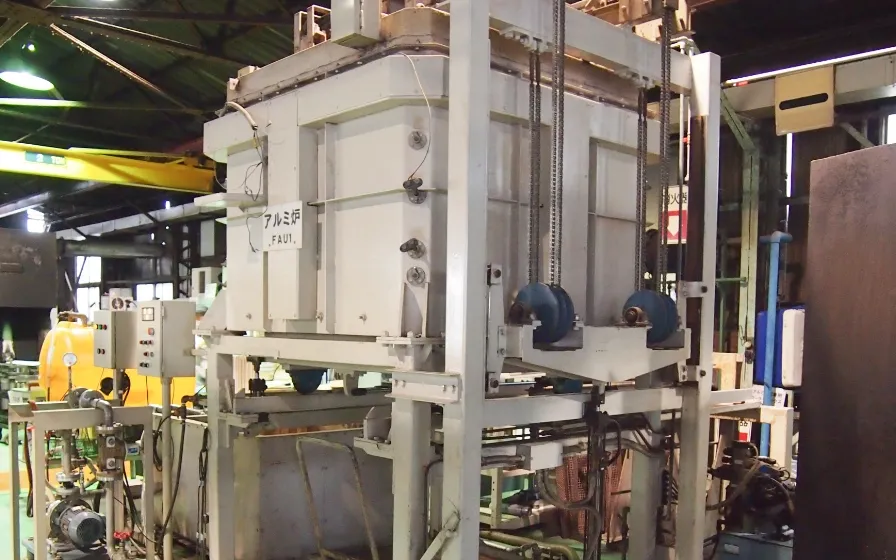
アルミ炉1号。この装置の導入により、アルミ合金の溶体化処理ができるようになった。
さらなる認定、さらなる空機部品、さらなる熱処理
三菱重工業(株)名古屋航空宇宙システム製作所の特殊工程(P-2020)および富士重工業(株)宇都宮製作所の特殊工程(MIL-H-6088)の特殊工程認証を取得する。
ISO9001の取得、品質の組織体制へ
ISO9001の認証を取得する。
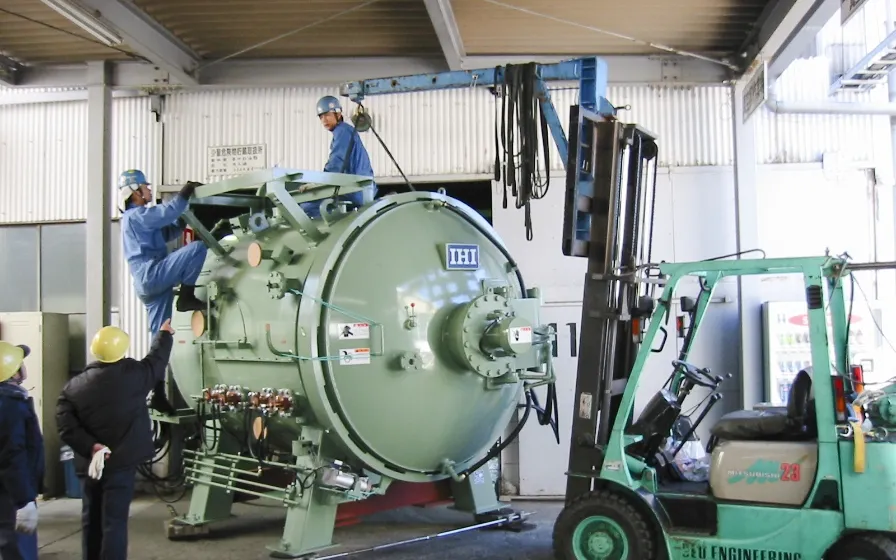
ISO9001を取得した同時期に導入した、当時最新鋭の真空8号炉、搬入の様子
デジタル化で実現した
多品種小ロット生産体制
作業指示システムソフトウェアをバージョンアップし、信頼性の向上を図る。
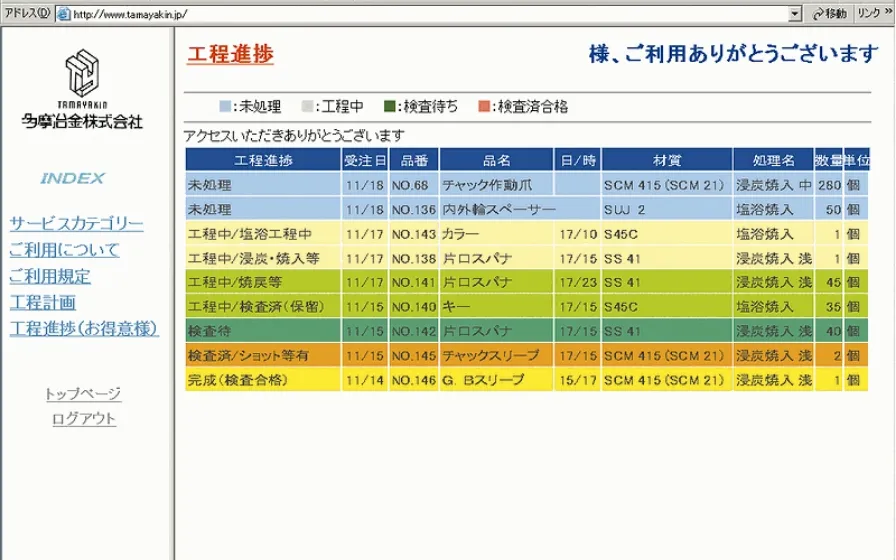
当時としては画期的で取材も受けた、工程進捗システムの画面
創業者の意向もあり、現在ではスタンダードであるトラッキングシステムなどにも、IT黎明期より積極的に取り組んできた多摩冶金。2001年のシステム改変では、さらにインフラも整い、職人技を数値化して熱処理工程の温度指示などを自動化することにより、多品種小ロットへの対応を省力化した。また、熱処理設備の制御システムを自社改修、設備管理システムの構築、熱処理工程の記録などにIT技術を最大限取り入れ、完成品からはその品質の判定が難しい熱処理、すなわち「特殊工程」の信頼性を向上させた。「お客様にとってより良いサービスとは」を追求し、改革を恐れず技術で課題を解決しようとする姿勢も「多摩冶金らしさ」の表れだといえよう。
詳細を
防衛部品の受託開始
住友重機械工業(株)の特殊工程(MIL-H-6875)の特殊工程認証取得、防衛省装備品の熱処理を開始する。
中国東北地方「大連」への進出、機械工業の基礎を支える
中国大連に子会社「多摩冶金(大連)有限公司」を設立、中国において熱処理受託加工を開始する。
総敷地面積13,000㎡。資本金2億6千万円(2007年増資し3億4千万円)。
当時、この地域では熱処理産業の数、質ともに乏しく、地域の機械工業の発展に必要とされていた。特に大連に進出した日系製造業に対し高品質熱処理を提供し、日系製造業の生産現地化に大きく貢献した。
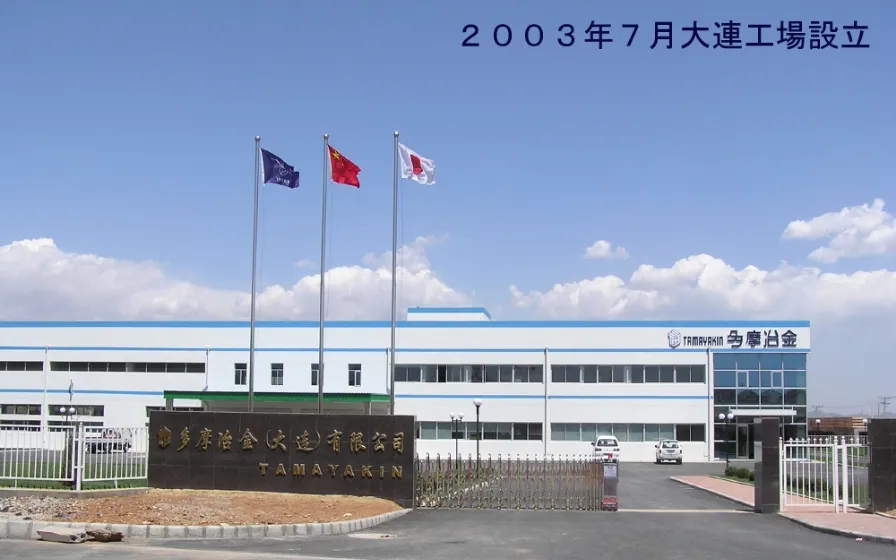
大連工場設立(2003年7月)
製造業における国内の空洞化が課題となる中、多摩冶金でもさらなる状況の悪化に備え中国進出を決意。時を同じくして、元研修生であった白氏からも声がかかり、現地視察や上海での展示会出展など、事前調査を進める運びとなった。その過程では、大連に工場を構える日系企業を中心に、複数の企業から「有力な熱処理工場がなくて困っている」という切実な訴えと同時に、多摩冶金に対する期待値の高さを実感。
フィージビリティ調査などの結果も踏まえ、「大都市ではなく、大連なら規模的にもマッチする」と判断し、多くの企業から期待を受けながら大連に熱処理工場を構えることとなる。
以降、日系の自動車産業を柱に、中国からあらゆる国々へ「日本の熱処理」を伝える拠点として、大連での事業は現在も右肩上がりの成長を見せており、工場の規模も拡大の一路を歩んでいる。
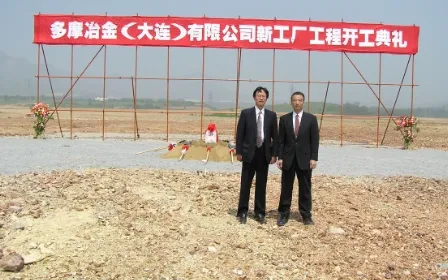
大連工場開工式に立ち会う、後の総経理
・白と2代目・山田仁
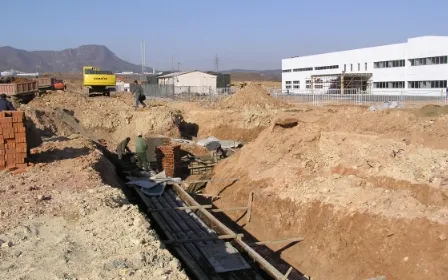
大連工場建設現場の様子
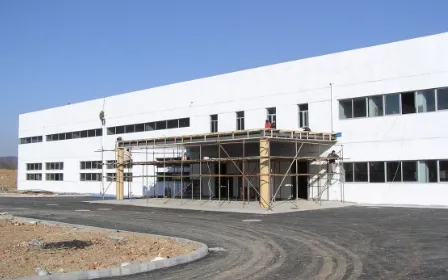
大連工場建設現場の様子
大連工場が最初に手がけたのは、本社が主力としていた部品の熱処理ではなく、部品を鋳造する金型自体の熱処理であった。当時の大連を含む東北エリアには、素材のポテンシャルを引き出せるほどの高度な熱処理技術を持つ工場がなく、部品メーカーのみならず鋼材メーカーも多摩冶金の活動に期待を寄せていたのだ。
そのため、ノウハウのない金型熱処理分野であったが、業界大手メーカーよりトップクラスの技術教育を受けることがかない、生活の中で活用されるステンレスや鋼製品の鋳造を担うプレス金型からプラスチックやゴム製品の鋳造を行うプラ金型などの重量が小さいものから、重量1tクラスで技術的にも難易度が高いダイキャスト金型まで、幅広くこなせるまでに成長。多くの期待と協力を得ながら、着実に基盤づくりを行っていった時代である。
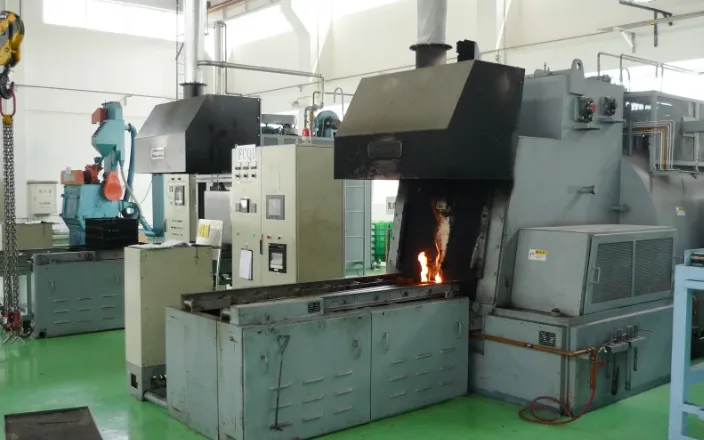
大連工場内設備
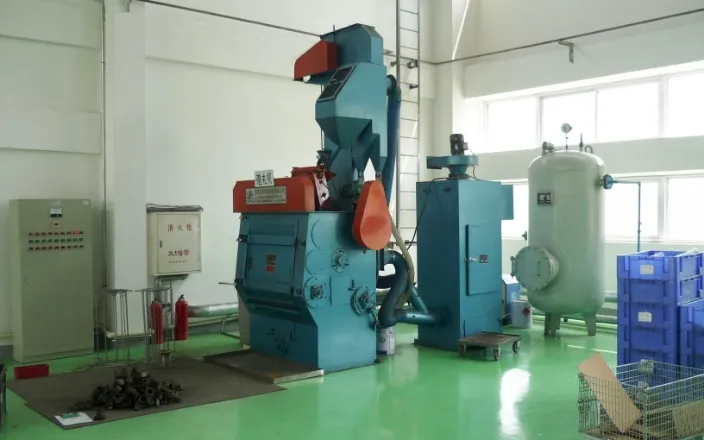
大連工場内設備
詳細を
大連工場、多品種小ロットから量産部品の世界へ
自動車部品、建機部品、電気部品、グローバルフィールドでの活動。
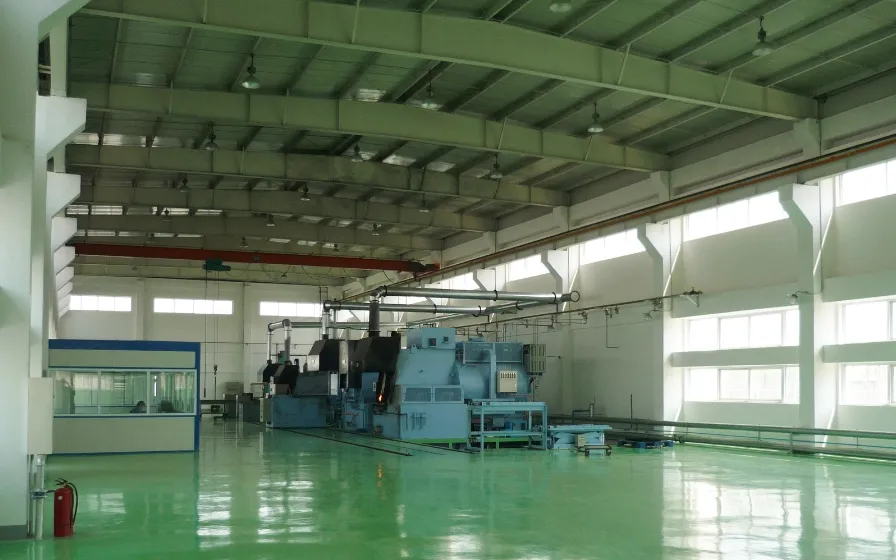
敷地の広い大連工場の様子
大連の主な量産実績
日立金属株式会社金型熱処理認定工場となり共立精機(大連)有限公司(本社共立精機㈱)のダイキャスト金型の熱処理開始。
富士電機大連有限公司(本社富士電機機器制御㈱)のブレーカー部品の熱処理開始。
大連林精密鋳造のABB社ロストワックス製電気部品の熱処理開始。
リョービ圧鋳大連有限公司(本社リョービ㈱)のダイキャスト金型の熱処理開始、自動車エンジンブロックアルミダイキャスト部品のインライン熱処理開始 。
詳細を
大連工場、電気・電子・機械部品の量産スタート
大きな発展を見込めないことも事実であった。その状況を見て、代表の白は新しい分野への参入を決意。いよいよ、東京本社の主力としている部品の熱処理に取り組むこととなる。
当時、中国国内の熱処理技術における品質は低く、メーカーは自社内、あるいは数キロも離れた都市部の工場へと品物を運び入れていた。そのような背景もあり、ここでも急速に受注件数が増加。電子・電気・機械部品を中心に、幅広く量産部品の熱処理を受託することで、新しい時代を築いていく。東京本社で長年培ったノウハウをベースに、多摩冶金の本領を発揮した新しいステージの幕開けである。
大連の主な量産実績
浸炭、雰囲気焼入れの導入、量産部品が開始(マイク、スター精密、ABB)。
大連東芝機車電気設備有限公司(本社㈱東芝) の機関車用モーターケースの熱処理。
瀋陽NSK精密機器有限公司 (本社日本精工㈱)のボールねじ部品の熱処理開始。
詳細を
開拓期|2004~
「いざ航空業界へ!」
3代目社長の奮闘
2004年より専務として営業活動に従事した3代目社長の手腕により、
業界トップ企業と手を携えて名実ともに航空業界の多摩冶金として成長を果たした時代。
ISO14001の認証を取得
ISO14001の認証を取得する。
リーマンショックからの切り返し、いざ航空業界へ!
塩浴工場跡地に航空機部品熱処理に向けた新工場を建設。
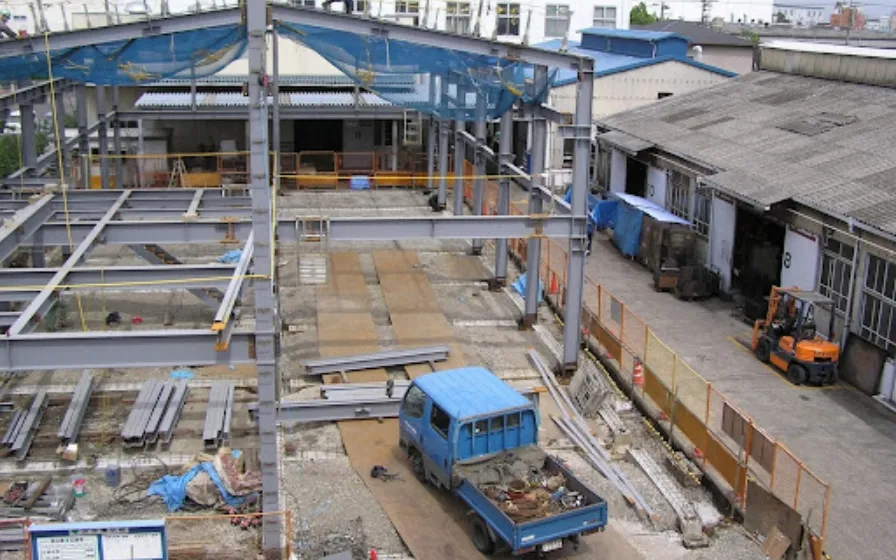
第1工場建設
新しい時代を迎えるため、創業時から稼働していた塩浴熱処理加工場を廃止。業界のニーズに合わせて早期に体制を整えられる場所を確保する。この決断が功を奏し、塩浴工場跡地には2011年より順次、次世代の柱となる航空機部品の熱処理設備が徐々に整えられていった。以降、この新⼯場では、新型旅客機のエンジン部品や、制御部品などを⼿がけていくこととなる。
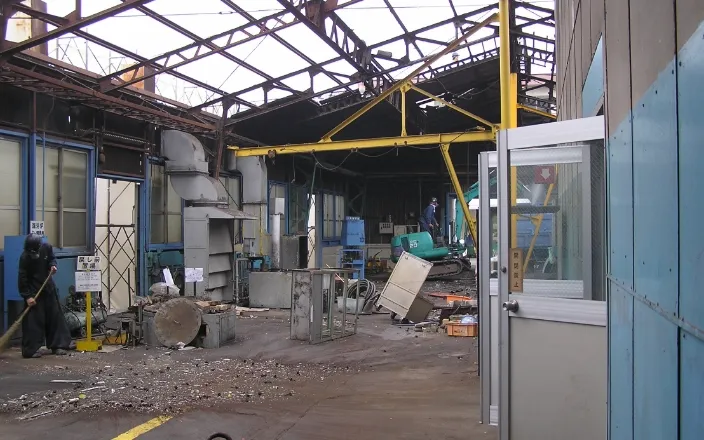
塩浴工場解体の様子(2007年)
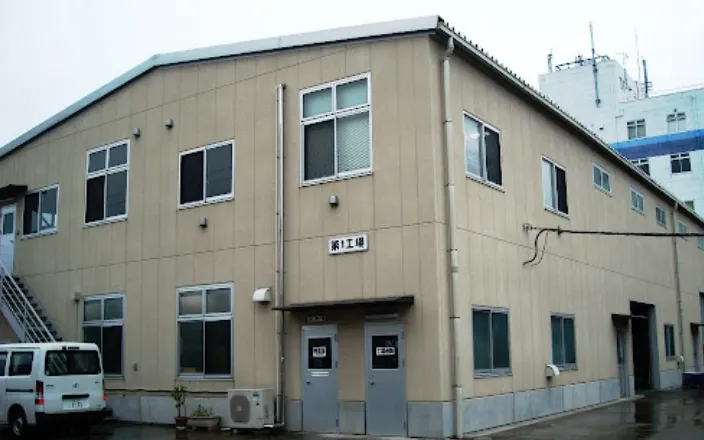
武蔵野工場
詳細を
技術集合体「アマテラス」設立メンバーに
技術集合体「アマテラス」の設立メンバーとして、航空機部品生産のコンソーシアム活動を開始する。
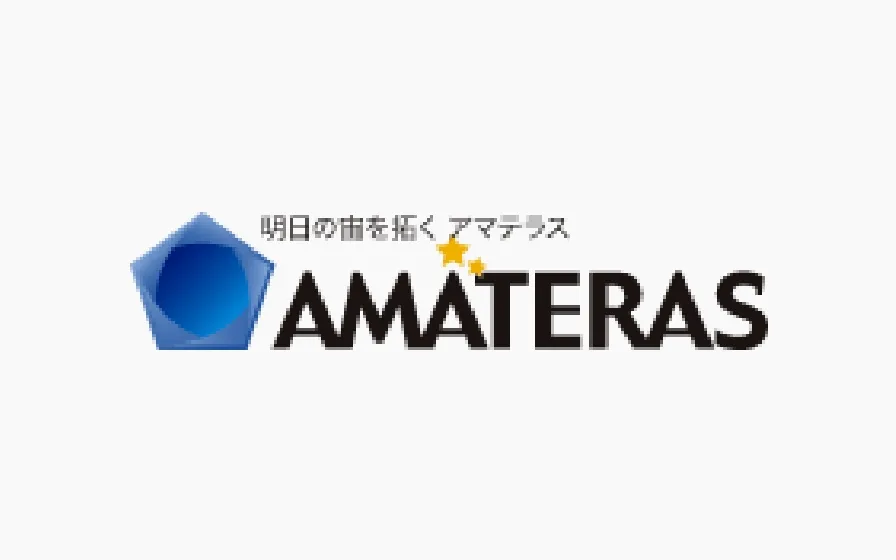
アマテラスロゴ
「アマテラス」は、次世代の航空宇宙産業の一翼を担う企業ユニットとして、東京都が主導で起こした東京地区の先進技術を持つ「航空宇宙部品製造企業連合」である。勉強会からはじまった当初は、300〜400もの企業が参画していたが、そのうち10社がアマテラスのユニットメンバーに選抜される。名だたる業界大手企業が名を連ねる中、熱処理部門で見事選抜された多摩冶金は、航空宇宙産業の先端を行くメンバーの一員として、新しいスタートを切った。
ここでの活動を通じ、多摩冶金は今までになかった強力な人脈とネットワークを築くこととなる。以降、様々な出会いを経てJIS Q 9100の認証やNadcapの取得へと舵を切り、着実に航空業界の中核企業として歩みを進めていく。
詳細を
大連工場、自動車部品の量産体制を確立し飛躍へ
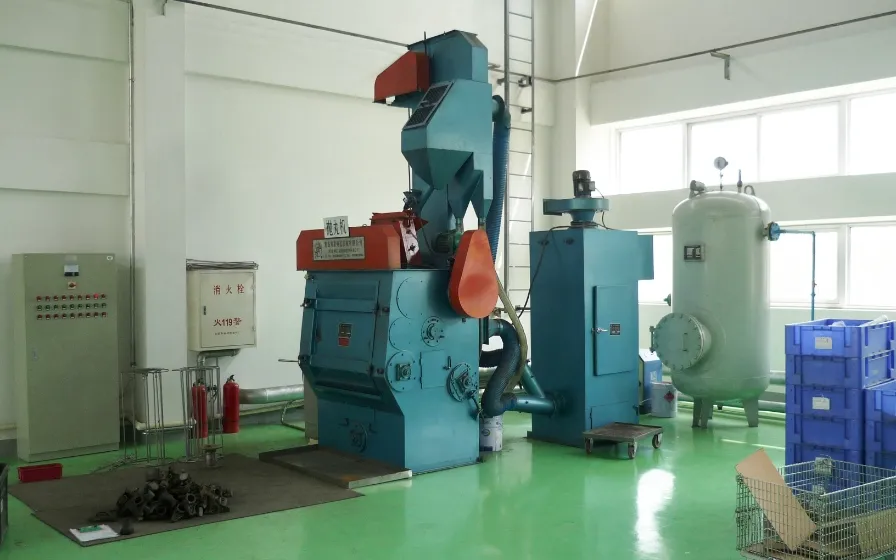
大連第2工場設備搬入
大連岐阜加藤精密加工有限公司(本社㈱ギフ加藤製作所)アイシンAW向け自動車部品熱処理開始
大連精工電子有限公司(本社セイコーインスツル㈱)の自動車部品の熱処理開始
ISO14001 取得
TS16949 (後のIATF16949) 取得
リョービ圧鋳大連有限公司工場内に熱処理部門を設置
THK遼寧精密工業有限公司(本社THK㈱)のLMガイド部品の熱処理開始
江蘇省常州市に多摩冶金(大連)常州分公司を設立、リョービ圧鋳常州有限公司(本社リョービ㈱)の自動車用アルミダイキャスト部品のインライン熱処理開始
金型、電子・電気・機械部品の熱処理に加え、2009年以降は、品質保証管理面でも難易度の高い自動車部品の熱処理を手がけるようになった大連工場。実はここでも、大手メーカーからの強い期待とサポートが、新しい一歩を踏み出すきっかけとなっている。
以降、2010年には自動車産業の国際的な品質マネジメント規格TS16949(後のIATF16949)を取得し、本格的に自動車産業に参入。時期を同じくして、中国国内では自動車製造台数が急速に伸びており、国内年間生産台数2994万台を記録した2017年まで、多摩冶金への需要増加も同じ曲線を描き右肩上がりで拡大の一路を歩んでいく。中国経済の発展とともに、大連工場も確固たる基盤を築き上げた時代である。
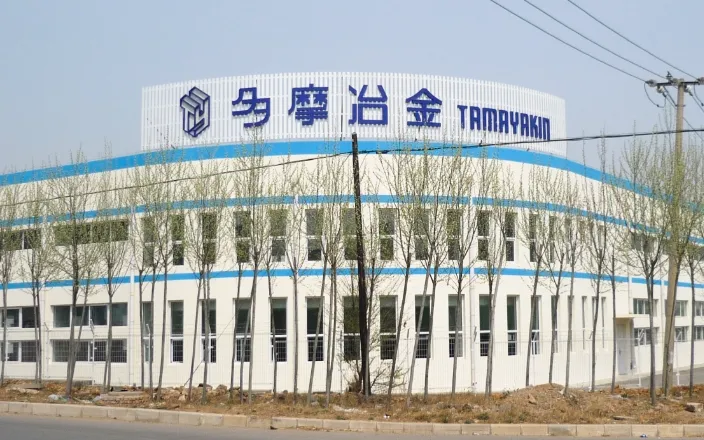
大連工場開業から5年以内に竣工した第2工場
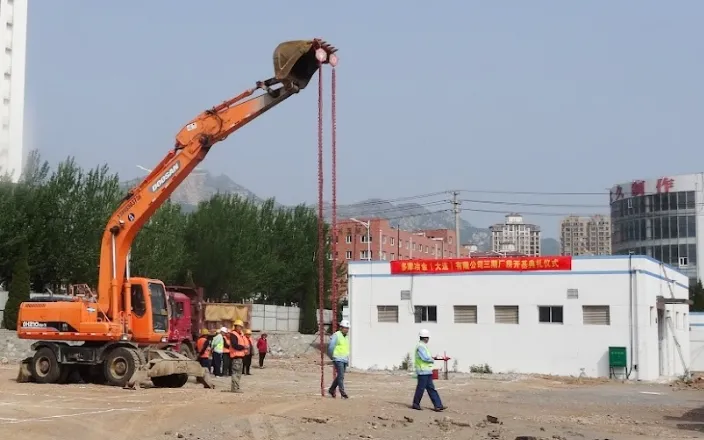
大連工場開業から5年以内に竣工した第2工場
詳細を
極めろ、航空機部品!
熱処理認定取得への道のり
航空機産業への参入時は大きな変革を求められることが多く決して楽な道ではなかった。

当社にとっての航空機産業の日の出はリーマンショックの危機感から始まった。
JIS Q 9100の認証を取得
JIS Q 9100の認証を取得。
新工場に航空機部品熱処理に向けた最新設備を導入
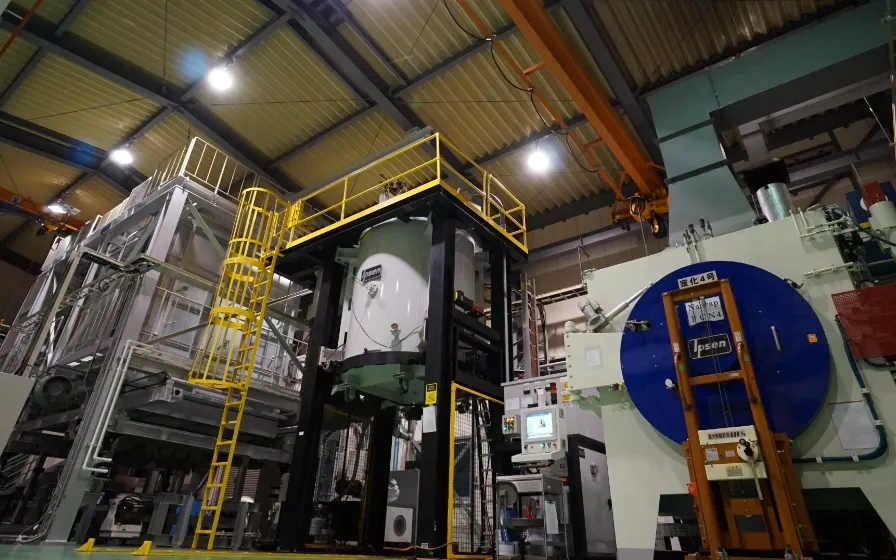
民間航空機部品市場への参入を目標に導入したドイツ・米国製の最新設備
Nadcapの認証を取得する
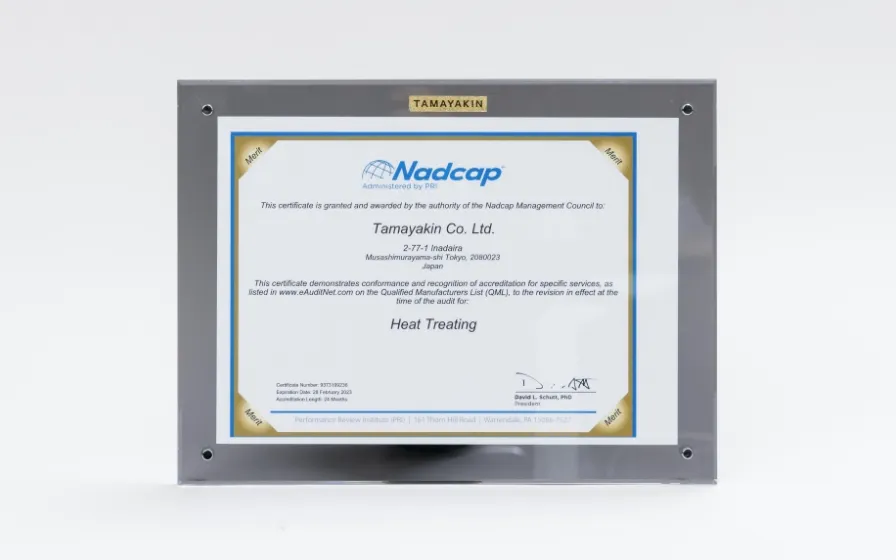
Nadcap認証
航空機エンジンPW1100G向け部品の量産が開始。
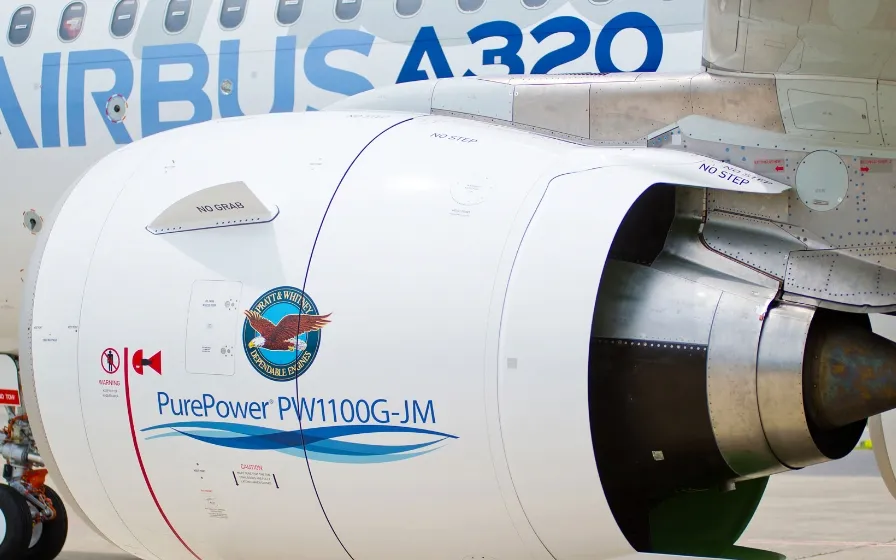
量産受注となった、A320 neo 向けのPW1100Gエンジン
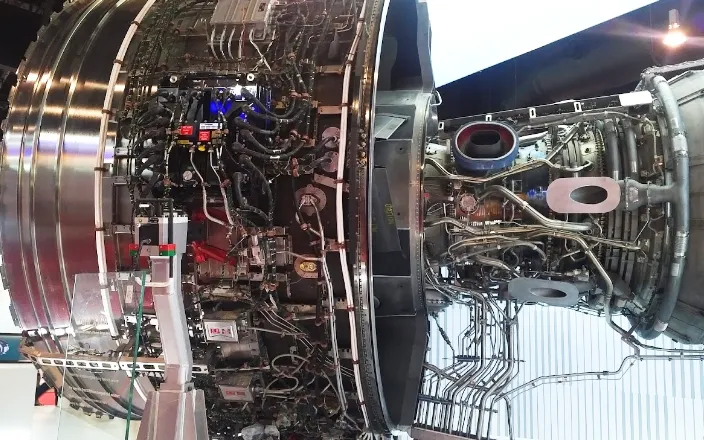
2017年より熱処理を受託加工しているロールスロイス製 航空機エンジン Trent XWB
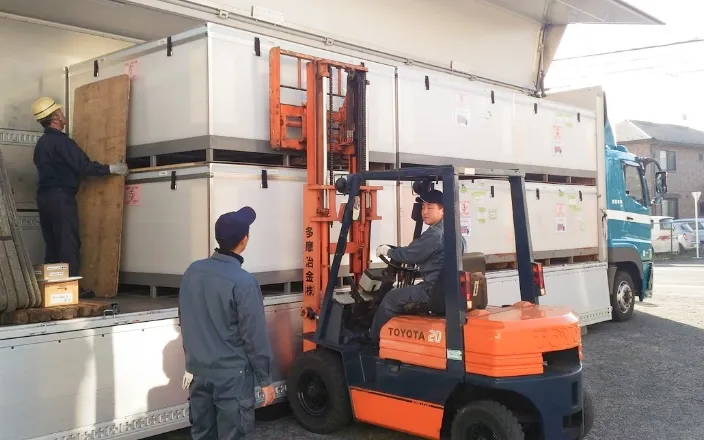
梱包された製品を大型トラックで出荷している様子
詳細を
航空機エンジンPW1100Gの増産体制に向けて広島事業所が開設
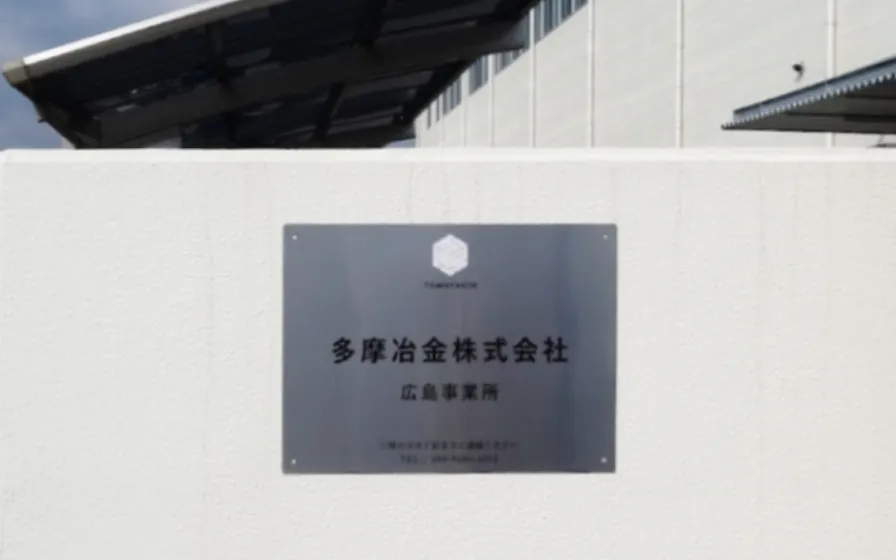
広島事業所、入り口看板
航空宇宙・防衛産業に特化した品質マネジメントシステムに関する国際規格「JIS Q 9100」は、世界の航空宇宙・防衛産業でグローバルな部品調達基準として採用されている。航空宇宙・防衛産業において製品・サービスの安全性を確保し信頼性を向上させるためのマネジメントシステム規格であり、その取得は非常に困難を極めるため、当初は国内で認定を取得している企業はごくわずかしか存在しなかった。
そのような中、多摩冶金はJIS Q 9100が求める品質マネジメントシステム、および後の航空宇宙産業界の国際的な工程認証プログラム「Nadcap」の取得に向け、社内の組織体制の強化、業務プロセスの可視化、コンプライアンスの順守などあらゆる側面から組織改革に取り組んでいく。
半面、「多摩の町工場」からの脱却は容易ではなく、働き方や仕事に向き合う姿勢の変革が求められた社員からは、反発の声も生まれたが、それは次第に「他ではできない仕事をする」という意識へと変化し、プロフェッショナルとしての誇りや尊厳、強いチームワークを育んでいった。
詳細を
ロールスロイス社の
熱処理認証を取得する
ロールスロイス社の熱処理認証を取得。
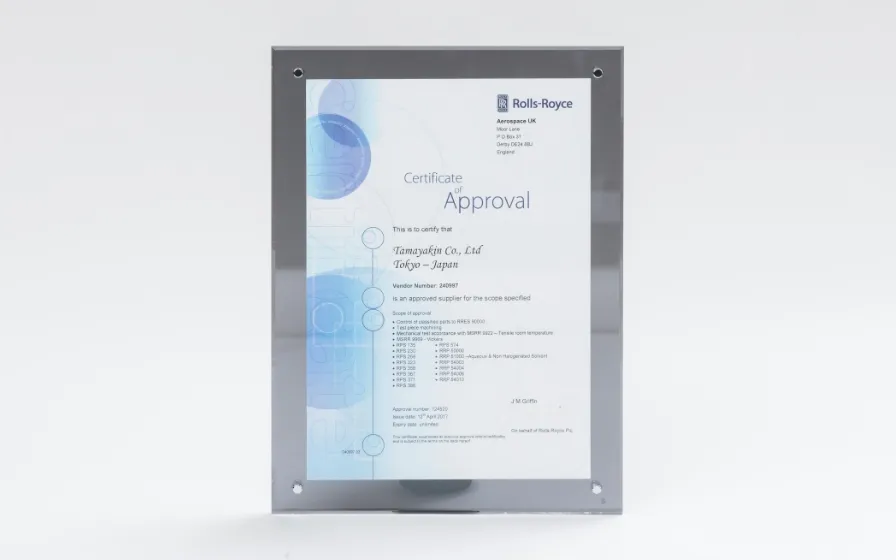
ロールスロイス社の熱処理認証
大連工場がNadcap認定を取得
大連工場がNadcap認証取得。
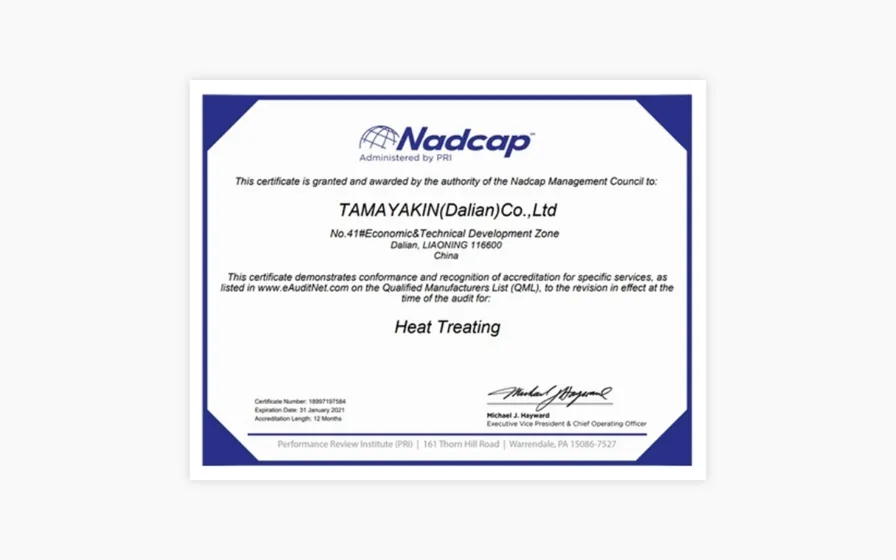
大連工場のNadcap認定
大連工場の主力は、引き続き自動車部品であることに変わりなく、設備投資も継続的に行っていく中、次なる時代への足掛かりとして代表の白氏が選んだ道は、東京本社がすでに実績を残していた航空宇宙分野である。
2019年には、日本国内でも取得が難しいとされているJIS Q 9100に匹敵するAS9100取得、続いて翌年にはNadcapの取得にも成功。この短期間での躍進には、東京本社一同が驚きを隠せなかった。
自動車部品は内需が中心だが、航空機のニーズはグローバルに広がる。現状では、飛行機備品の受託はごくわずかではあるものの、この一歩は大連工場の可能性を大きく広げ、新しい歴史の幕開けにつながると確信している。
高度な認定を取得し、地域の産業に貢献
ISO9001 取得
ISO14001 取得
IATF16949 取得
AS9100 取得
Nadcap 取得
詳細を
第二次成長期|2016~
「目指せ100年企業!」
3代目兄弟の次世代を担うモノづくり
2004年より専務として営業活動に従事した3代目社長の手腕により、
業界トップ企業と手を携えて名実ともに航空業界の多摩冶金として成長を果たした時代。
新卒採用元年
新卒採用社員、第一期生が入社する。
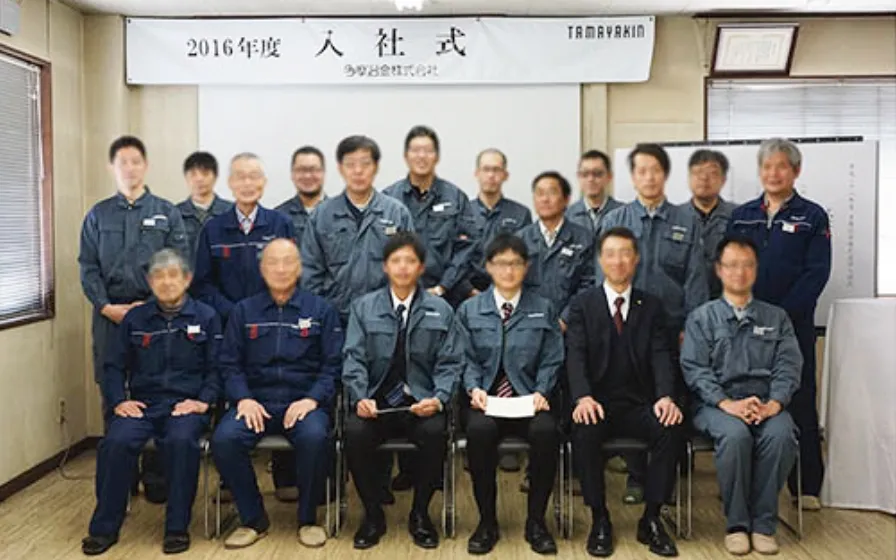
創業以来初となった大卒新卒社員の入社式
3代目社長就任、兄弟で目指す100年企業へ
3代目社長・山田毅が社長に就任。弟である山田真輔は副社長に就任。それぞれの海外経験やバックグラウンドを活かし、100年企業を目指した新生多摩冶金が発動。
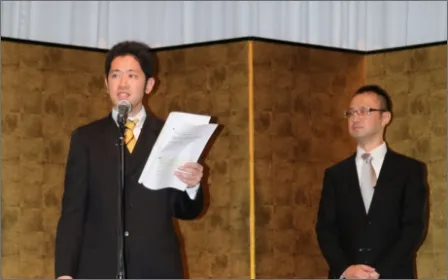
65周年
2017年8月に3代目社長に就任した山田毅は、前職時代に経験した中国駐在員などの経験を活かし、持ち前の経営手腕を発揮していく。幼少期より、父であり現会長の山田仁の背中を見て育っているだけに、商いに対する興味関心は人一番強く、大企業ではなく中小企業で実力を発揮したいと、自ら入社を希望した。
入社後の3年間は現場で技術を学ぶも、その視点は徐々に「事業をどう拡大していくか」へ向けられ、アマテラスの参加など自らの判断で新しい道を切り開いていくこととなる。
詳細を
南工場建設へ
東京本社工場から徒歩10分の場所に、事業継続と拡大を目的に土地を取得し、20年後を見据えた多摩冶金の中で最大規模となる南工場の建築が始まる。
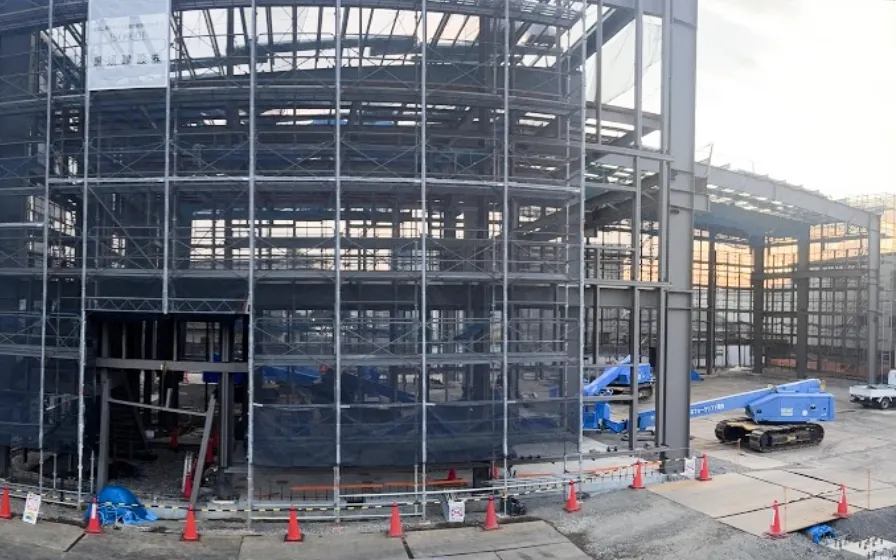
建設中の南工場( 2022年1月の様子)
「多摩冶金 100年企業」を目前に控え、3代目社長が見据えているのは「その先の未来」だ。そして、今回新設した南工場は、その土台を担う重要な役割を持つ。
1つには、熱処理だけでなく、製品の工程すべてに関われる工場を目指していること。これにより、熱処理を中核に、素材から最終形状までを担える新しいビジネスラインが確立する。
2つ目には、まだ見ぬ未来の製造業を支える工場となること。カーボンニュートラルが主流となる時代を見据えた設備選定に加え、新たな自動車「空飛ぶ車」を筆頭に、「風力発電」「医療」「環境」など、これまでにないスケールで、製造業を広く支える存在を目指している。2021年を皮切りに、3代目社長が描く新しい多摩冶金のストーリーが、今まさにはじまろうとしている。
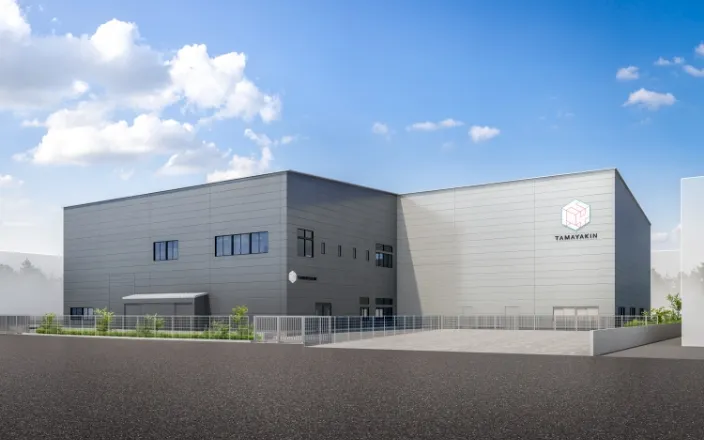
南工場完成予定図
詳細を
お問合せ
お気軽にご相談ください
お気軽にご相談ください